Knowledge is power, but are you collecting the full array of data points you need to guide supply chain and network management decisions?
Chances are, you’re not. There are organizational and market-driven reasons why important facts about network infrastructure, maintenance, and overall operations are often opaque. These barriers can be difficult to overcome, but the advantages of greater transparency make it worth the investment of time and effort to obtain and track comprehensive network information.
What Network Operators Don’t Know—and Why
The sheer complexity of large networks makes full transparency challenging to achieve. In most cases, dozens of vendors and suppliers and countless internal departments operate in a more or less siloed fashion. The parties include engineering and design specialists, site development personnel, and installation technicians, as well as spares management, maintenance and repair, and reverse logistics groups involved in building, commissioning,
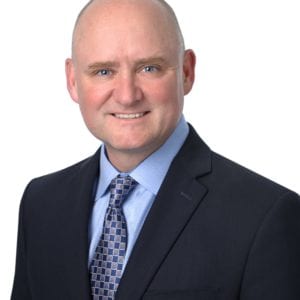
operating and decommissioning network elements.
Compiling basic information from such a wide variety of sources can be a herculean task. Exacerbating matters, commercial considerations lead some vendors to resist efforts at information sharing. Hardware manufacturers are not inclined to expose design or manufacturing defects, as unwanted publicity hampers sales and damages the brand reputation. Similarly, field services companies would prefer not to highlight deficiencies in technicians’ knowledge, training and practices.
Profit motive frequently compels support providers to take steps to maximize the volume of hardware sent in to be fixed, rather educating clients about avoidable repairs. And some contracted maintenance providers may even direct completely recoverable assets to the waste streams, because they deem it cheaper for them than undertaking a refurbishment.
These and other factors leave network operators at a loss for hard data on such topics as percentage of repairs completed under warranty, mean time to failure, or root cause analysis for particular equipment in varying environmental conditions. Lack of information means lack of insight into where and how efficiency, productivity, performance, and uptime can be enhanced.
Why Network Intelligence Matters
For network operators, coming to know what they don’t know may seem a Socratic detour, but there are real-world advantages to identifying and rectifying information gaps. Take for example the typical product failure.
The events that unfold usually go something like this: The Network Operations Center (NOC) identifies a failure, opens a trouble ticket, and dispatches a technician. The field services engineer troubleshoots the issue and takes corrective action. In many cases, the response will involve installation of a replacement product and, therefore, depletion of the spares pool. A new spare is ordered from the central repository, while the defective part is sent out for repair.
Without capturing and comparing the information generated at each stage in this process, the network operator will remain in the dark about, and therefore unable to improve on, key decisions. The waste occurring across the wireless industry is surprisingly high. For instance, we have found that 30 percent of repair requests are completely avoidable. Even back-of-the-napkin math indicates any large network operator stands to save tens of millions of dollars each year, not only cutting costs on the repairs themselves but also on spares inventory, truck rolls, logistics, freight, tower climbs and beyond. And, this does not even include the risk of customer loss.
Issues as basic as software misconfiguration and corruption, login problems, and dirty connections frequently send functional network hardware to the repair center. The solution is often as simple as the problem—providing better resources to field technicians. What’s required is a feedback loop with actionable and transparent data, whereby information from the repair specialists informs technician training and operations support.
This means that network operators must track significant data over time, so they can spot trends, identify common issues, target outliers, and craft the right response. In some cases, the company might offer an upskill session on an optical transceiver to deployment personnel in the Eastern Region, where installation errors are much higher than average, or the data could point to a manufacturing defect which is causing issues network-wide.
Repair-related changes are frequently low-hanging fruit for boosting ROI, but the power of data reaches further. Knowing more about network assets is critical to lifecycle management, so network operators can wring maximum value out of hardware investments, without overspending on maintenance for older equipment. In the reverse logistics arena, immediate alerts about decommissioned hardware enable those responsible for support contracts to remove the product from maintenance, and tracking the price that used equipment commands in the market can inform upgrade decisions. Accurate total cost of ownership detail can also improve procurement choices. With historical data, accounting for total service life, repair costs, spares availability and costs, uptime, and more, network operators may find the lowest bid isn’t always the most cost-effective and shift purchasing decisions accordingly.
Seize the Data
These are only a few examples but the takeaway is clear: Network operators need to capture as much information as possible at every touchpoint for each piece of hardware on which they rely. Doing so generally requires new tools and processes to enhance internal communications, documentation, and data accessibility, as well as a transformation of vendor/supplier relationships to prioritize and incentivize information sharing. Analytics solutions can then be used to translate high volumes of data into targeted, actionable insights.
The time investment shouldn’t be underestimated, but overcoming the barriers to transparency brings meaningful, budget-friendly upsides. Information sharing enhances trust within the organization and with vendors. Data-driven decisions improve the supply chain and increase operational efficiencies, productivity, and network uptime. And at the end of the day, transparency benefits wireless providers’ primary audience—the consumer. With more information, network operators are empowered to deliver greater performance and better features at a lower cost, maximizing competitive advantage and value to the customer.