From tractor maker to network operator; should we be surprised Deere & Company, in charge of the John Deere machinery brand, has snapped up five mid-band CBRS licenses in five counties in the US? Not really; not at all, even. It has a reputation for innovation in the field, where its machinery is getting rapidly smarter. It was always going to seize the chance to bring such digital wizardry in-house, when the FCC put the 3.5GHz band up for auction.
The firm has been running tests with private 5G for some time; the new spectrum licences, announced in September, cover four sites in Iowa (Black Hawk County, Scott County, Dubuque County and Des Moines County) and one in Illinois (Rock Island County); they cover its five biggest factories in the US. John Deere paid $545,999, and will build private 5G networks at each venue to spark smarter production.
It is searching for a partner for 5G radio and core networking gear, by all accounts; it remains unclear whether or not it will hand management of its new 5G networks to a third party, or absorb the discipline into its own IT functions. “The next manufacturing revolution is right in front of us,” said Tami Hedgren, the company’s manufacturing lead for tractors and combine harvesters.
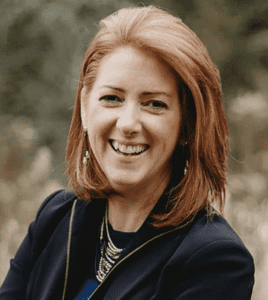
It has been installing sensors and running analytics to raise productivity and bring intelligence to its key production sites for some time, using existing networking equipment. But the prospect of 5G, it reckons, stands to raise its Industry 4.0 games, and put it in a position to “fully embrace” industrial IoT and “revolutionize” its factory operations. Rollout starts in 2020, it said; but the firm’s expectations are already high.
Jahmy Hindman, chief technology officer at John Deere, commented: “Our focus on tech goes way beyond the fields. It impacts every aspect of our business… Implementing 5G in our manufacturing facilities allows John Deere to make significant progress in our Smart Industrial strategy by turning factories into smart and connected manufacturing facilities – a critical piece of the industrial IoT.”
Hedgren said: “With smart factories, we will identify issues before they become problems and have solutions ready before they become disruptions. This will help make us more efficient and our customers more productive…. We’ve been doing some testing with 5G … and we see the benefits. It’s real time data where you need it at the right time, and it’s a totally different viewpoint than Wi-Fi.”
John Deere’s manufacturing facilities currently feature “miles of embedded Ethernet cables connecting Wi-Fi drop points in factory ceilings”, it said in a statement. “The facilities are faced with limited flexibility for set up and upgrades. Private 5G will allow [us] to design a more flexible, nimble and connected facility, creating opportunity for further advancement and greater efficiency that will transform the manufacturing process.”
The company indicated it will deploy 5G to bring automation and intelligence to the factory floor, with autonomous guided vehicles (AGVs) and collaborative robots (co-bots). Further demanding industrial applications, such as computer vision cameras and augmented reality (AR), and other digital-twin manifestations, are likely to come under consideration, too.
John Deere noted the potential role of wearables and real-time location systems (RTLS), for tracking assets and inventory, as well as staff, although certain of these may be supported by complementary short-range beaconing and mesh networks.
Writing in a blog post, Hedgren commented: “Our customers are looking for innovative solutions to be more productive and profitable. We’re innovating to meet their needs and revolutionize our industries. This starts with… smart connected factories, which use technology and data in manufacturing…. We’re already collecting the data. We need to pull it all together, so we can predict what’s going to happen and make decisions on behalf of customers.”
John Deere has been connecting its machines since 2011. “Connectivity has really changed the game for farmers,” Lane Arthur, director of digital solutions at the firm, told Enterprise IoT Insights last year. But the game has shifted, he said. “When we started, we collected data about the engine, the machine itself. That was valuable for customers. What has changed is the ability to understand the work the machine is actually doing.”
Computer vision and machine learning are new in farm equipment. “We have some today; we will have much more over the next five years.” In the new S700 series tractor, John Deere is using these capabilities, at the edge and in the cloud, to change the harvester settings based on the quality of the grain being collected – down to single grains coming into the machine, as well as yield volumes and moisture levels.
Lane said: “Let’s suppose we’re harvesting wheat; if the settings are wrong, we’ll have too many cracked kernels. In the past you’d check the kernels by sight, as they came in, and make the changes manually, with considerable skill. Now, that happens automatically – both the checks and the adjustments to the machine,” explains Arthur.
The company’s latest 32-row planters, planting 32 rows of a crop, have 15 sensors on each row unit, collecting data at a rate of five times a second, including about the volume of seeds, their placements, skips in the process, and the ground conditions as they are planted. “Multiply that out and we’re talking 2,400 readings per second.”