Farming is just outdoor manufacturing, says John Deere; the whole concept of ‘smart manufacturing’ is only novel to cloistered production, taking place indoors, out of the rain. Farmers have been at it for decades, already: connecting machines, processing data, bringing intelligence into the field. Because the dynamics of manufacturing food, outdoors, are out-of-control – the only way is to work around them.
The idea is not to be hostage to fortune – in the shape of weather, weeds, and commodities markets, as well as the kinds of mechanical errors and inaccuracies the modish Industry 4.0 movement is focused on. As well, the drive to automate processes and machinery, another ‘factory-of-the-future’ pursuit, is old news in farming. Driverless cars? Automated guided vehicles, for ferrying factory goods?
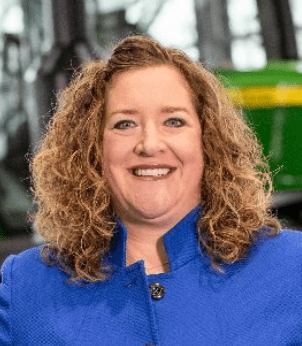
Tractors have been ploughing fields in perfect straight lines for decades, without much help from drivers.
The comparison with smart manufacturing, recently boosted in the US by the availability of CBRS spectrum for enterprise-geared cellular networks, is interesting. Deere & Company, in charge of the John Deere brand, has just snapped up five mid-band licenses to cover its five biggest factories in the US; four in Iowa and one in Illinois. The company paid $545,999, and will build private 5G networks at each, it says, to spark smarter indoor production.
But factory-based innovation is not where the company has made its name. At CES last month, the firm was back in its comfort zone: talking about its tractor-based tech, and, with prompting, how to bring this wizardry from the field to factory – from outdoor production lines running 72 rows across, sown and harvested with the seasons, to indoor lines running around the clock, producing equipment to go into the field.
At the other end of a video stream, Deanna Kovar, vice president of production and precision ag systems at John Deere, responds: “Precision agriculture has led the way. We’ve been leveraging the same technology stack in production-class farm equipment for 20 years, already. But we are applying the same mindset in our factories, now – to develop an equivalent tech stack to handle all the variability that comes with indoor manufacturing.”
The idea of farmers as Luddites is wrong, she says; John Deere’s record of innovation stands for the whole sector, going back 184 years, when John Deere, the blacksmith, “the man himself”, developed a steel plough “to cut through the deep black soil of the Midwest”. Three-quarters (76 percent) of all farming land in North America is planted with AutoTrac, John Deere’s GPS-based reference software to guide self-driving farm vehicles.
In the last 12 months, data from 230 million acres of farmland in 100 countries has been uploaded over cellular networks to the John Deere Operations Centre, the firm’s cloud compute platform and data dashboard. Kovar hinted at a future, where indoor and outdoor manufacturing is more closely integrated. “The vision is to tie a digital thread between these two production environments, which are somewhat separate today.”
She adds: “They have similar approaches around connectivity, monitoring, and analytics. At some point, they will join together, and allow farmers to make even better decisions, and take even better care of equipment.” Kovar is standing in front of a 72-tonne tractor, pulling a 16-row planter, at the John Deere factory in Iowa; this is the 8RX – the iPhone 12 Pro Max, the 7-Series (?) BMW, the Dwayne ‘The Rock’ Johnson of tractors. You get the idea.
But it is only the most-laden big-ticket route into smart farming; the company’s ‘precision ag’ business, she notes late on in the discussion, was founded as a retrofit affair, and John Deere is making various connectivity and any number of analytics-based sensors available to make even 20-year old tractors ‘smart’. “Every farm, every field, every machine is different. You don’t start from zero and go to 100 overnight; you take it step by step.”
But the 8RX represents a giant leap, to get to 100 percent, and the CES demo, which includes a VR tour of an Iowa ‘smart’ farm, is designed to show what is possible already in agriculture. Lots of it puts today’s smart factories in the shade; so let us recap. Kovar sets the scene: this is the company’s third year at CES, and it wants to talk about how tech is changing the process of planting seeds (its first two showings put light on crop harvesting and crop spraying).
We are online, of course, rather than in the Las Vegas convention hall. But John Deere’s strategy to send VR goggles to the world’s media, to showcase its digital pyrotechnics, is arguably more effective. The farm, the tractor, the tech – it is all very striking, and more real, actually, than sitting inside a static cab in an exhibition centre. But before Enterprise IoT Insights climbs into this virtual world, Kovar, gestures at the 8RX behind her.
The 16-row planter behind the tractor is topped with yellow tanks and threaded with sensors, to scatter seeds 20-30 inches apart, at a rate of 100 per second, in the right spot every time. The same unit, in the same movement, also digs trenches, removes “residue and dirt”, and covers it over again after the seed is planted. Even on screen, the two machines are massive. The planter goes to 72 rows, and up to 500 acres a day.
Kovar explains the challenge for planting, and for farming generally: to “break the paradigm between productivity and speed”. Until John Deere started harvesting new digital tech, planting seeds was restricted to a top speed of about 5mph; the new planters go to 10mph, with centimetre-level accuracy. Kinda slow? Maybe; but once strapped in, we are plunged into a pit (an underground ‘soil lab’), somewhere in a field in the Midwest, and promptly run over.
The tractor-planter races over us; it is pretty nippy. And then the software re-runs it at full speed, at 10mph, and you want to duck your head. “If we were in Las Vegas, we couldn’t drive a tractor over you,” says Kovar. The VR showcase, with live commentary, puts us alongside the planter, into the cab, way up in a ‘bird’s nest’ control room; each time, we get a view of how data is pulled from the field, processed in the cloud, and rained down as ‘insight’.
The ghost-in-the-machine is the connectivity, she says – carrying the data, between the twin production engines running in the field and in the ‘cloud’, processing crops and data, making machines and humans both work better. It comes two ways, for John Deere: GPS and cellular. The firm is one of just five in the world, she says – “not just in agriculture, but in the whole world” — that owns its own satellite correction system.
John Deere can get GPS accuracy to 2.5 centimetre, apparently; standard GPS positioning on a smartphone, for running maps, only gets you to five metres, says Kovar. “GPS makes sure we stay on those straight rows, when planting, and don’t overlap… It’s impressive we can deliver seed at 10mph; but it’s even more impressive we can adjust the delivery in split seconds, as the tractor speeds up and slows down.”
The company’s tractors run 2G and 4G to disseminate positional data, plus a mad array of sensor-based metrics from the farm. Data is rendered in the John Deere Operations Centre, and filtered down into farmer apps. “Farmers make thousands of decisions each year – some are seasonal decisions, some are day-to-day. You have to collect data about every acre of land, and understand how those decisions result in higher yields at the end of the year.”
The VR tour takes in the ‘connected cab’, for a driving simulation. Kovar suggests the tractor is a better driver than me; I am mildly offended, and mutter something about the controls. But the point is clear: John Deere has been doing self-driving for years, since long before it became a mission statement for California carmakers, and a way to blow public money for smart-city demonstrators.
Farmers have to farm when they have to farm; in the US, they have a 10-day window, apparently, to get crops in the ground. “Mother Nature is not always the most obliging,” says Kovar. “Timing is super critical; you can lose 10 percent of your revenue for every day you miss.” Autonomous driving is a ‘god-send’ for a farmer on an 18-hour shift, with one eye constantly on what is happening behind the cab, where the action is.
As noted above, three quarters of farming land in North America is ploughed and planted with AutoTrac. “Twenty years ago, it was hard to produce straight rows [of crop] in a field. Now, with self-driving and GPS, you don’t see any crooked rows anymore. Driving is one of the first things we took out of drivers’ hands, to focus on other things,” says Kovar.
In the cab, there are a bunch of displays, with live feeds about various happenings about the place. But the best view of the production equipment in both the field and the cloud is up in the ‘bird’s nest’ – a rather impressive viewing platform, which looks out across the fields, where tractors are at work, and where a series of popup dashboards provide a neat visualisation of the company’s operating centre.
So we get a yield map, which can be rendered at farm-level, field-level, even plant-level; it shows inputs against outputs, and works like a scorecard, says Kovar, for “decisions made through the year”. We are shown, with popup visuals, how the various tractors and machinery “talk together”, and not just with the farmer, but with a whole long-tail of mechanics and dealers to act on live data to run predictive maintenance and reduce downtime.
The farmer is not always directly required; jobs and decisions are delegated outwards, via this orchestrated two-way data flow out of the farm; the farmer, himself, can tune in on his iPhone, as required, while he is at his kid’s soccer game, and the farm takes care of itself. That’s the dream, both for farmers and for factory managers.