The latest developments in cloud-based AI and edge computing, coupled with 5G’s enhanced bandwidth, are about to mobilise robots like never before and unleash a manufacturing revolution, explains Richard Cockle, Global Head of IoT, Identity and Big Data at GSMA.
Factory automation is on the cusp of a revolution thanks to the roll-out of services built on the potential of 5G; its next-generation wireless connectivity will enable manufacturers to truly streamline their activities through the application of smart technologies. Many businesses around the globe are already looking to leverage 5G’s capabilities to rationalise their operations and create agile manufacturing facilities better suited to modern, demand-driven commerce.
For example, by harnessing its augmented bandwidth and faster speeds, 5G can help industrial robots unplug their cables and move freely within the confines of a factory. This will not only help reduce operational costs but may also boost output. In fact, 5G is expected to contribute an additional $960 billion to the global economy by 2030, according to the GSMA’s latest Mobile Economy Report, with nearly $366 billion of that coming from manufacturing.
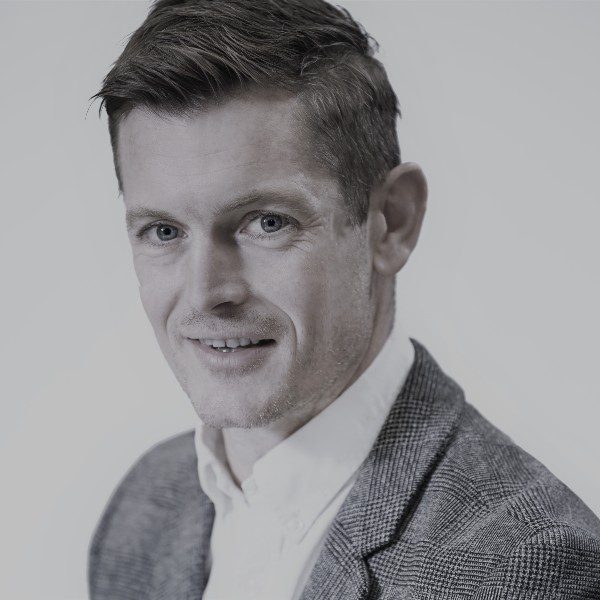
The secret to this transformation will be the use of artificial intelligence (AI) at the network edge or in the cloud. Put simply, by relocating software, such as image recognition software, from a robot to the edge or cloud, it can combine and process image data from all of the robots in a factory, ultimately reducing costs and improving decisions. Manufacturers can, as a result, unleash the full potential of robotics and reshape conventional factory floor processes.
Proof of concept
Together, robotics, 5G and AI are a powerful combination. However, this revolution is not yet at the ‘unplug and play’ stage because deploying wireless robotics in an industrial environment can be complex and costly. Many of the AI algorithms, 5G networks and chipsets needed to ensure an efficient and timely implementation need more time to develop.
As such, most industrial 5G robot deployments are still at the proof of concept (PoC) stage, and we are about two or three years away from realising the full benefits with more commercial use cases – but the potential productivity gains are clear to see.
There are already AI implementations coming to market that can improve the recognition software associated with a robot’s onboard camera to deliver next-generation object tracking and machine vision. In this way, 5G-enabled robots are set to make factories significantly safer as they will be able to detect workers in their vicinity and take appropriate actions to operate safely.
There are good examples of how all of these elements are coming together. Thundercomm is using 5G to connect robots at a major automobile plant in China. Running on wheels, the robots transport spare parts, equipment, and materials around the factory floor. No longer dependent on cables for communication, the 5G robots can safely operate in every corner of the factory, supported by enhanced face and scenario recognition software.
Future developments
In time, manufacturers will be able to model, install and ramp up robotic systems, confident that they will perform as designed – a scenario that’s already starting to coalesce. As a result, enterprises of all sizes will be able to reduce overheads, increase productivity and efficiency, avoid costly mistakes, and ultimately transform their operations.
We already know that robots can work longer and faster than people – by aligning these benefits with AI and 5G, they also become increasingly flexible, freeing up employees from high volume, low value, repetitive tasks so they can complete others more effectively.
While there are barriers to making this a reality, 5G momentum continues as operators look to digitalise operations and remain resilient. The cost of equipment is falling, which in turn is accelerating the adoption of the technology. Manufacturers have also started altering their approach to 5G beyond a one-dimensional level to reap the full benefits. With a well-thought-out strategy in place at the start of the Industry 4.0 journey, the smart, automated factory of the future can begin to materialise.
The good news is that the technology for 5G implementation is already within our reach. This is evident across a wide range of novel applications outside of manufacturing and heavy industry. Wireless robots are already being used by some Chinese hotels and restaurants to deliver goods to customers, a small glimpse of what’s to come.
It is also clear that if businesses want to remain competitive in this smart future, they need to plan for it now. The union of cloud, edge computing, AI and 5G connectivity is about to transform a wide range of manufacturing processes, and enterprises that don’t adapt and adopt risk losing out in the battle of the robots.
Learn more about innovative use cases for 5G on the GSMA’s 5G Transformation Hub.