Globalization is shifting. Reshoring and nearshoring are the new trends, driven largely by a desire to be less dependent on China, but also by the supply chain fragility revealed during COVID, as well as geopolitical shifts, and the drop in domestic demand due to growing inflationary pressures.
In recent months, demand for electronic components sold in China decreased by 20 percent (March), 22 percent (April), and 25 percent (May), according to the Supplyframe Commodity IQ Demand Index. Meanwhile, “the pace of globalization has plateaued since the global financial crisis,” as Savills Research reports. Global trade growth was just 2.7 percent last year, according to The World Trade Organization, which forecasts that global trade growth will drop down to 1.7 percent for 2023.
But new product designs that rely on electronics components are ramping up worldwide, not just in one or two countries, which is a healthy sign. And nearshoring and reshoring are now providing manufacturers that rely on electronics components to build products – such as 5G and 6G network infrastructure equipment – with the opportunity to get smarter in how they handle manufacturing and how they develop talent to drive better outcomes for businesses and the communities within and around them.
Digital twin and greenfield opportunities
In November 2022, Deloitte said that 62 percent of US manufacturers have already begun building nearshoring and reshoring production capabilities. The Wall Street Journal recently reported that the construction of new manufacturing facilities in the US reached $108 billion in 2022.
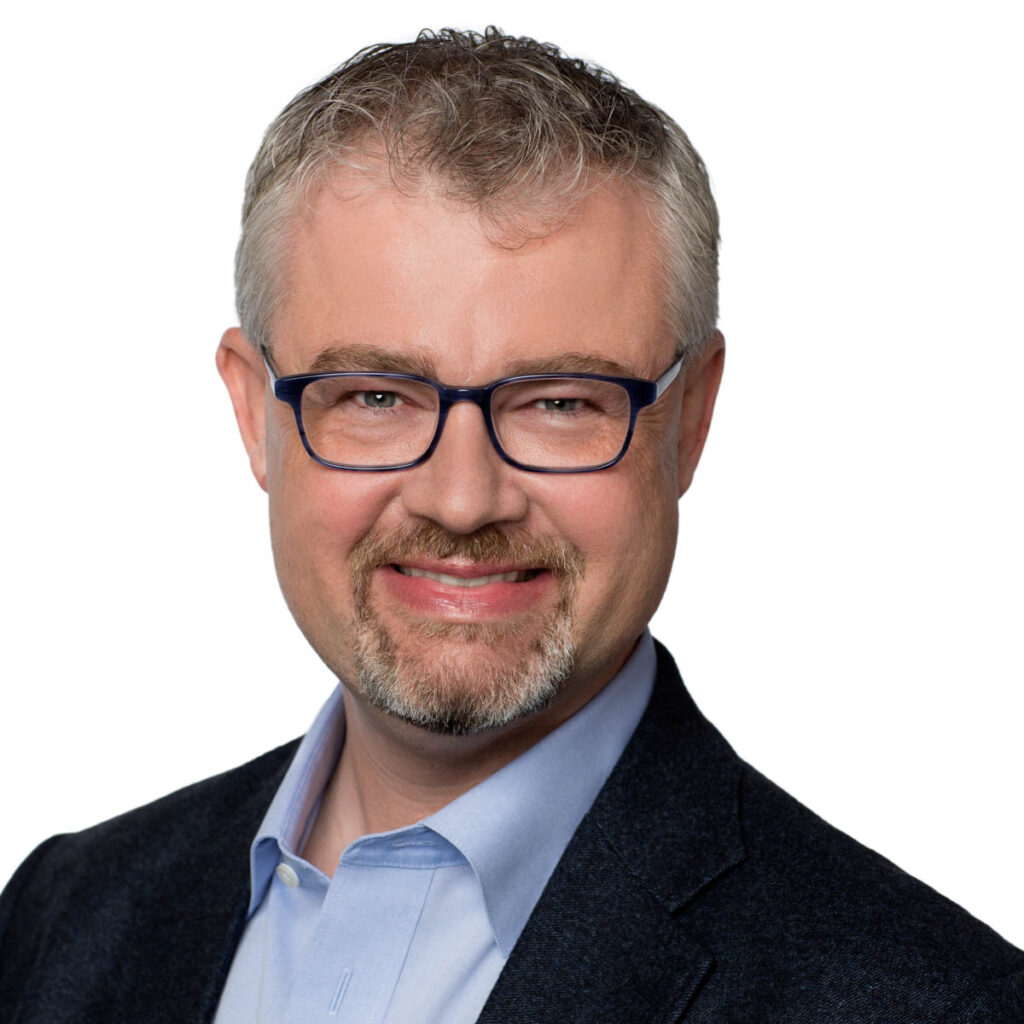
Such greenfield efforts present manufacturers with the opportunity to use digital twin technology to design, simulate, measure, and refine both product and assembly process performance up front – before companies even start to build their new production facilities. As Siemens told CNN: “If we can transfer all the problems that we have in our real world, put them in the digital world, do our iterations, see what-if scenarios, and bring that back into the real world, there’s a lot of ROI, return on investment, to be had.”
Converting existing manufacturing plants, particularly more legacy ones in places like China that were designed to be more people-intensive because of assumptions about lower-cost labor, is a big challenge. But greenfield factory builds make it much easier for manufacturers to leverage the power of automation, data and the internet of things, and new forms of intelligence.
Automation is key to reducing waste, increasing reliability, and driving better ROI at manufacturing plants. For example, computer numerical control (CNC) machines enable manufacturers to use pre-programmed computer software to control the movement of factory machinery and tools. Universal Technical Institute explains that CNC machining provides a level of accuracy, consistency, and efficiency that is impossible with manual processes.
KPMG reports that 71 percent of global companies acknowledge raw material costs are their No. 1 supply chain threat for 2023. Franco Oliaro, CEO of ROJ Electronics, says that around 80 percent of the value of a product can come from the materials with which it is made, and too many scraps can kill a manufacturer’s profits. So, manufacturers must control both their processes and their materials.
Automated materials management helps manufacturers track and access raw materials and implement just-in-time dispatching of raw materials to avoid production stoppages. New forms of intelligence that provide visibility across the electronics supply chain can also prevent production slowdowns and stoppages by helping manufacturers ensure that they have the semiconductors and other components needed to meet their production needs.
Balanced investments and the labor gap
Mexico has become a favorite nearshoring manufacturing site for companies in North America. Europe is looking to such countries as the Czech Republic, Hungary, and Poland. And India, where Apple and Samsung are looking to expand their electronics production, has the highest growth potential in Asia for expanded investment to create new manufacturing sources.
But many newer markets with expansion opportunities face a skills shortage. Allied Market Research expects the global factory automation market, valued at $242.5 billion in 2021, will reach $558.8 billion by 2031. However, it says the limited availability of professionals is among the prime factors restraining the factory automation market growth. The ability to train and develop skilled workers remains a significant challenge.
Private-public partnerships investing in reshoring and nearshoring should work to balance their investments and incentives between semiconductor fab development, research and development, and developing a skilled workforce. This template could also be applied in telecoms.
There are also opportunities to leverage new technologies as blueprints to develop manufacturing talent. For example, smart manufacturing capabilities like additive manufacturing networks employ an ecosystem collaboration approach. This provides new ways to collaborate, from design through fabrication, having a trusted source of supply, and ensuring that the intellectual property is protected.
Additive manufacturing also offers the benefit of supporting specialized supplier ecosystems for small-batch efforts.
Project-based delivery and multi-tier visibility
The edge-based computing approach of new wireless networks is a hyper-local innovation model for which companies build out infrastructure on a project basis, as needs arise. So the idea of shortening delivery and logistics lead times is not just about cutting costs, it is about gaining the ability to achieve project-based goals to meet just-in-time schedules. The ecosystem around 5G-to-6G conversion involves project-based delivery capacity.
Many of these programs are scheduled over time, and require tier-two and tier-three electronics, specialized final assembly, and the development of new manufacturing locations. But people in the wireless industry are over indexing on final assembly locations. They need to remember that the wireless industry, like many sectors, relies on a multi-tier supply chain where dependencies, constraints, and bottlenecks can occur at any tier and that the risk of complications – particularly from the electronics components perspective – remain very high.
The future is bright for nearshoring and reshoring. But the complexity of global supply chains, particularly electronics value chains, and dependence on sources of supply from China will persist. That means companies must still have visibility into the risk across their value chains to make the most intelligent decisions about the components and suppliers they choose.
Richard Barnett is the chief marketing officer and SaaS company Supplyframe. He drives go-to-market and communications strategy for the company’s industry ecosystem and Design-to-Source Intelligence (DSI) Solutions. He has more than 25 years of leadership experience in strategic marketing, sales, and product management.