The full connectivity of digital infrastructure and the intelligent platform are the twin engines for smart factories to accelerate the intelligent manufacturing upgrade, according to Summer Chen, Vice President and General Manager of Branding and PR Strategies at ZTE.
During a presentation at the Manufacturing DX Summit hosted by GSMA at MWC Barcelona 2024, Chen delivered a speech on the topic “Accelerating the Upgrade of Intelligent Manufacturing with Twin Engines Drive,” offering a perspective on the transformation and upgrading of smart factories.
Summer Chen first elaborated on the concept that a smart factory is a collection of highly automated and intelligent management. She emphasized that the core goal of smart factories as business entities is to achieve cost reduction, efficiency increase and quality improvement, with corresponding technologies and means serving this goal.
To achieve this goal, she proposed a new transformation paradigm called “Twin-Engines Drive.” On one hand, this involves the upgrading and renewal of infrastructure to achieve comprehensive and efficient digital connectivity in factories; On the other hand, an integrated intelligent platform is built on the comprehensively upgraded digital infrastructure to connect data and capabilities across the entire chain, driving the intelligence of production and management, and enhancing cost reduction, efficiency increase, and quality improvement through intelligence.
The ZTE executive pointed out that the introduction of the industrial private network based on 5G and 5G-A, industrial PON, and edge computing can significantly simplify the current situation of multiple connection methods and protocols coexisting in the production site through full-scenarios, full-elements, and full-capability connections.
Chen added that the establishment of an integrated intelligent platform will also vigorously promote the data flow throughout the entire chain of the factory, thereby eliminating data islands between IT/OT systems in traditional production, and achieving intelligent decision-making. This paradigm offers practical benefits by enabling factories to quickly introduce innovative applications such as machine vision and AGV, leading to cost reduction and efficiency improvement in individual processes, Chen said. Moreover, it assists in production operation decision-making through global intelligence, elevating the overall intelligence level of the factory, she added.
Chen also shared the practical results of ZTE’s application of the “dual-wheel drive” paradigm, a transformative approach applied in the fields of new energy vehicle manufacturing and electronic manufacturing in recent years. At the Geely Group’s Lynk & Co Zhangjiakou manufacturing base, the implementation of the 5G intelligent distribution solution has resulted in an impressive increase of approximately 67% in production efficiency per year. Similarly, at ZTE’s Global 5G Intelligent Manufacturing Base, where comprehensive digitalization and intelligent applications have been leveraged, the output per unit of 5G products surged by 113% and delivery time was reduced by 48%.
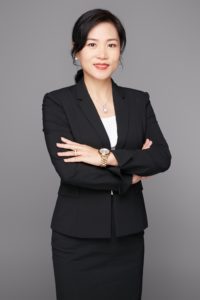
Summer Chen also said that she envisions a future where smart factories will evolve towards collaborative intelligence, functioning as “organisms.” “The intelligent platform and digital infrastructure will drive various intelligent applications resembling smart brains and sensitive nerves. Moving forward, ZTE is committed to actively collaborating with industry partners across diverse fields, aiming to jointly accelerate the scenario-based landing of intelligent applications and promote quality growth across the entire industry,” she said.
In related news, ZTE, in partnership with Wuhan Iron and Steel Co. (WISCO) and China Unicom, announced that their joint project “5G Fully Connected Smart Steel Factory” earned the “Best Mobile Innovation for Connected Economy” at the Global Mobile (GLOMO) Awards during MWC Barcelona 2024.
Since 2020, the collaborative efforts between the partners have led to the establishment of the “5G Fully Connected Smart Steel Factory” project. This project has now evolved into the largest 5G private network in the global steel industry, achieving a 5G coverage of 99% within the factory premises.
Leveraging this 5G private network infrastructure, the project has deployed 25 steel applications across six major scenarios. These applications span intelligent logistics, production control, digital equipment management, energy and environmental control, quality control, and safety management.