Generative AI hype hinges on its novelty: new creative possibilities, business applications, and growth opportunities. For manufacturers, this technology has the potential to streamline supply chain management, help plant managers proactively address maintenance problems and drive efficiency across manufacturing sites.
Today’s industry leaders are exploring applications of generative AI to stay competitive and keep their data – and their production lines and supply chains – protected. However, while 70% of manufacturing leaders are investing in generative AI, only 44% report a net positive return on their investments, according to a recent Kyndryl survey exploring the readiness paradox.
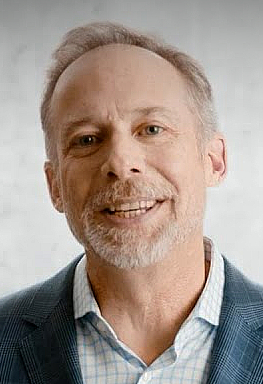
To harness generative AI’s game-changing capabilities and start bridging this gap, the manufacturing sector must first sharpen its focus on the familiar.
In 2025, manufacturers will look to the technologies already fueling transformative gains in the sector to unlock generative AI’s full potential.
Ubiquitous connectivity – which enables the ability to share data anywhere, at any time – edge computing, and last-mile technologies are emerging as key digital enablers that will accelerate transformation and help generative AI live up to the hype.
Addressing long-standing challenges
Because AI models depend on the data they’re fed, manufacturers won’t maximize their investments until they can overcome data silos and safely collect and transmit meaningful information between the back office and the plant floor. The industry also lags in modernization, which creates additional roadblocks to AI success. To cite two examples, more than half of manufacturing leaders are concerned that their IT tools or processes are outdated, and 68% struggle to keep pace with advances in technology.
With significant safety and financial risks involved in manufacturing disruptions, companies often prioritize incremental change over major IT overhauls. And they may neglect costly upgrades as they fight to stay on the right side of razor-thin margins.
Yet the sector’s aversion to risk presents its own risks: outdated systems and processes can create security gaps, increase the likelihood of business disruptions and lead to compliance issues and financial penalties. After decades of stopgaps and skipped upgrades, further postponing modernization efforts will only exacerbate the problems caused by a patchwork of components that don’t communicate well and make it difficult to gain a holistic and precise snapshot of a company’s operations.
Unlocking gen AI’s potential
To move into the future, forward-thinking manufacturers are investing in ubiquitous connectivity by embracing private 5G networks, the latest generation of Wi-Fi, and hybrid models that provide dual benefits, paving the way for more beneficial use of generative AI.
With higher bandwidth and lower latency, these network technologies improve data collection and analysis, enabling the rapid exchange of data as sensors transmit readings at much shorter intervals. This constant, real-time monitoring helps manufacturing leaders make more informed decisions – about when to schedule maintenance, for example, or replace aging equipment – and run a more efficient plant. What’s more, a layer of security that includes firewalls, encryption, and multi-factor authentication can be built into the network to better protect increasing volumes of data as IT and OT converge.
Ubiquitous connectivity also makes it easier to integrate edge computing, which brings data processing and storage closer to its source. Considering the mountain of data generated by facility-wide monitoring systems and the remote nature of some of these environments, manufacturers can significantly reduce expenses and increase processing speed by taking a local approach to their data. Because of its decentralized nature, edge computing delivers insights faster, instantly alerting staff to concerns that they can more quickly address.
With ubiquitous connectivity and edge computing in place, manufacturers can more accurately track conditions throughout the supply chain. Especially when powered by extended-life batteries, these last-mile technologies provide consistent, reliable, real-time data that can help operators manage their assets more effectively as they comply with new regulations. The cost of implementing these technologies is also dropping due to expanding IoT capabilities, longer battery life, inexpensive sensors, and powerful new encryption algorithms.
For manufacturers, harnessing the capabilities of these familiar network and edge technologies will offer new opportunities to accelerate generative AI adoption. But proactive companies will also invest in their employees to unlock generative AI’s potential. By prioritizing continuous learning and AI upskilling opportunities, companies can ignite innovation and empower people to engage in more strategic, productive, and fulfilling work.
With the right skillsets, improved data sourcing, and more secure transmission, companies will be poised to capitalize on generative AI in 2025, unleashing insights that prepare their businesses to navigate the future with confidence. But the fundamental lesson of the rise of gen AI will remain relevant for years to come: the promise of new technologies depends on the strength of their underlying foundations.