We have the know-how, we have the data, and now we have the AI – was the message from Siemens, the grand old aristocrat in Germany’s Industry 4.0 scene, at the opening of Hannover Messe, the country’s giant old Industry 4.0 trade jamboree – which runs this week (March 31 to April 4), and which has worked in recent years as a useful industrial reality-check for the niche telco hype about enterprise transformation that has just wafted out of MWC. But AI is different, of course, and even such a sober bunch as this is giddy with the idea that the traditional engine room of the global economy will be jacked-up and revved-up on a new AI speedball. The difference, now, says Siemens, is that the AI mix is just right for Industry 4.0.
Opening the event, Siemens announced a new industrial foundation model (IFM) in collaboration with Microsoft, which draws on a digital archive of its own ancient libraries of domain-specific production know-how in order to optimize industrial engineering and automation. It is the first of its kind in the field, the company said, and will integrate in production systems with its digital twin (industrial ‘metaverse’) software, as well as its Industrial Copilot generative-AI tool, and new virtualised programmable logic controllers (vPLCs). The latter have now been deployed to control production at an Audi factory in Germany, it added.
The new foundation model will process and contextualize 3D models and 2D drawings as well as industrial data and technical specifications, it said, and make data-based recommendations to “alleviate the skilled workforce gap and increase operational excellence”, it said. Roland Busch, president and chief executive at Siemens, remarked: “We have domain knowhow – we understand our industries. And we have the data. Together with AI, this is a winning combination.” He emphasized the need for a new “operating system” for Germany with “less bureaucracy, [and] more and faster innovation”. Siemens stated: “The country has a once-in-a-generation opportunity to reinvent growth.”
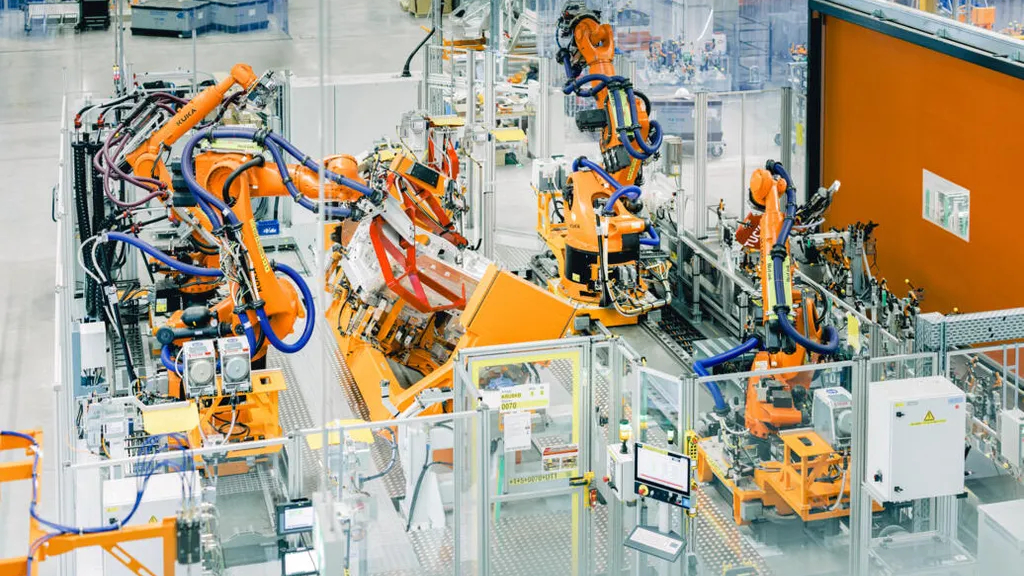
The “biggest technological lever” is industrial AI, it said – which underpins the company’s big internal strategy, about being “ONE Tech Company”, where AI is brought to bear variously across its big product portfolio, housed in its Xcelerator marketplace. The company has also unveiled a sequence of big partnerships, too – with Accenture, AWS, and Nvidia, plus more with Microsoft. It has created a dedicated industrial AI practice with Accenture (called Accenture Siemens Business Group) with 7,000 staff between them, which will develop and market joint AI solutions that use the former’s Xcelerator products and the latter’s “data and capabilities”.
They want to accelerate digital transformation across industries with a focus on “high-growth” regions, they said. Siemens also has a new ‘metaverse’ deal with Nvidia to plug the latter’s compute solutions into its Xcelerator products. In Hanover, the pair are showing their work on the German outfit’s digital-twin service, Teamcenter Digital Reality Viewer, which uses its US counterpart’s Omniverse graphics platform to raise its visualisation, simulation, and immersion capabilities. Users of its Simcenter STAR-CCM+ computational fluid dynamics (CFD) software can now run more simulations without losing accuracy using Nvidia’s accelerated computing and CUDA-X libraries.
Similarly, Siemens is using Nvidia AI to enhance its Industrial Co-Pilot for real-time video analytics to help reduce operational downtime. Meanwhile, Siemens and AWS have signed a deal to advance smart and sustainable infrastructure. Its Building X digital-building platform is being shown at Hannover Messe with the US firm’s cloud services and AI capabilities, including its Amazon Nova and Amazon Bedrock products, provisionally to increase efficiency and reduce costs. Separately, Siemens has integrated its Industrial Edge data-collection tool with Microsoft Azure’s cloud platform – to do the same (improve quality, efficient etc).
But the company’s big news is really about this domain-specific AI / IFM with Microsoft and new software-defined OT / vPLC with Audi. In the case of the latter, Siemens has deployed virtual Simatic S7-1500V PLCs on an assembly line at Audi’s Böllinger Höfe plant in Heilbronn, Germany. Siemens said: “Instead of hardware-based controllers close to machines or robots, virtual controllers are running in a data centre kilometres away.” Siemens is the first company worldwide to get a safety certificate for a vPLC from Germany’s TÜV technical inspection association, it said. Audi is also using AI solutions from Siemens for optical inspections of weld spatters on vehicle bodies.
Audi will roll out the virtual PLCs in the body shop at its Neckarsulm factory this year. Gerd Walker, in charge of production and logistics at Audi, said: “A virtualized shop floor is a key enabler for flexible production… to rapidly respond to market changes and optimize manufacturing.” Cedrik Neike, chief executive of Siemens’ digital industries business, said: “Controllers are the ‘brains’ of machines and factories. We are… bringing them to the cloud.” The S7-1500V provides the same functionalities as a regular hardware PLC. It works with the company’s automation (Totally Integrated Automation; TIA) portfolio and can be engineered via its web portal.
As well, the Siemens Industrial Copilot has won the Hermes Award 2025, awarded by Deutsche Messe for a cutting-edge innovation at the opening of Hannover Messe. “It is the first generative AI product for industrial environments across the entire value chain – from design, planning, and engineering to operations and services,” said Siemens. Neike called the award “one of the industry’s highest honours”, and said: “We’re transforming how humans interact with machines. It’s about speed and simplicity. This will make the benefits of automation widely accessible, simplifying for instance machine code generation and making complex tasks easy and fast.”