California-based software developer FogHorn provides edge intelligence software for industrial and commercial IoT applications.
The company has signed with auto-parts maker ADVICS to deploy its edge compute software to enable real-time analytics and artificial intelligence (AI) as part of its “smart factory transition”.
It is also working with German car maker Porsche to develop a real-time video recognition solution, using multi-factor authentication, for unlocking and securing vehicles. and NTT-subsidiary NTT Data to re-sell on-premise analytics and AI to the manufacturing, telecoms and energy industries.
Here, we catch up with Ramya Ravichandar, the company’s vice president of products, to discuss its views and experience of the market, including work with ADVICS and also Japanese industrial electronics company DAIHEN.
How are factories bringing intelligence to the production line?
Industrial IoT plays a critical role in the digital transformation of the manufacturing industry. Through advanced technologies, such as edge computing and streaming data analytics, equipment maintenance and operations can be monitored in real-time to improve operational efficiency, increase yield, and optimise performance.
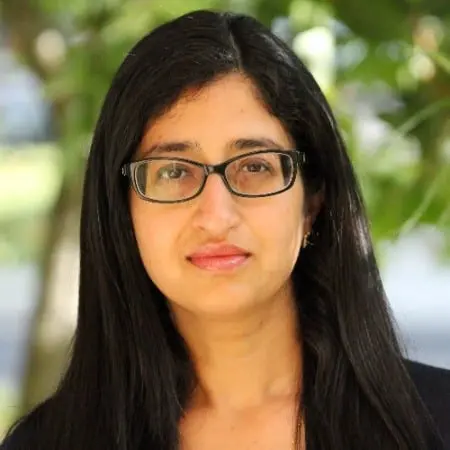
As an example, centrifugal pumps are widely used across all industrial and commercial sectors. Industrial sensors allow pump pressure and health to be monitored constantly to avoid conditions such as pump cavitation, where there is a sudden reduction in fluid pressure. This ultimately results in lowering the boiling point of liquids, converting the vapor bubbles back into its liquid state, and initiating shock waves that can damage pump components.
To avoid this, pump sensors can send a signal to the main system to automatically reallocate the flow of fluid to a different pump, preventing damage and reducing maintenance and costly downtime due to pump cavitation.
What of the role of advanced analytics – and the interplay between artificial intelligence (AI) and machine learning (ML)? What are the challenges?
By implementing ML, organisations can increase productivity, efficiency, and cost-savings. But machine learning models degrade over time because of [changing] environmental conditions. They are normally trained only on subsets of available data, and so may not provide accurate results after a period.
In a factory, for example, an ML model might be deployed to detect defects on part of an inspection assembly line. But after a few months, it is unable to detect the defects correctly and loses accuracy. AI on the edge benefits organisations as it identifies and triggers the re-training of inaccurate machine learning models.
If an ML model delivers unreliable results, an edge platform with AI capabilities can automatically trigger the re-train the model, and re-deploy it once completed. AI insights can enhance ML models and significantly improve their predictive capabilities – pushing tuned models back to the edge in a constant closed loop, reacting to changing conditions and generating higher quality predictive insights.
What are the results? How are these technologies impacting efficiency and productivity?
FogHorn has some real-world examples, where it has helped manufacturers realise gains through edge computing.
For instance, ADVICS, an international supplier of automotive brake systems and components, was looking to enable real-time visualisation and analytics of its manufacturing to drive increased productivity. It collected data through PLCs (programmable logic controllers), and wanted to get actionable insights without spending hours of analytical work to parse through the data and develop weekly performance reports.
So it designed an environment which unified the data collected from each manufacturing process using edge computing. Additionally, it used out of box tools from FogHorn Lightning to enable visualisation and analysis in real-time.
As a consequence, the company can complete real-time processing of approximately 1,150 pieces of streaming data at intervals of 200 milliseconds from each of its PLCs. With FogHorn, it has cut the time spent on data source identification by more than three days – and time-spend on compiling actionable insights for weekly performance reviews from five hours to just one hour.
Another example is DAIHEN, a leading Japanese industrial electronics company. The company wanted faster ways to analyse sensor data from devices measuring material conditions and reduce the need for manual monitoring at its Osaka factory. It deployed edge computing software in collaboration with Energia Communications to automate monitoring of its industrial transformers, and harness the power of its industrial data.
DAIHEN leveraged an RFID infrastructure to track manufacturing and team productivity and installed sensors to monitor the factory conditions, including temperature, humidity, and dust levels.Within six months of deployment, the Osaka plant achieved 70 per cent coverage with the RFID-based tracking system and expects to reach 100 per cent coverage.
Since implementation, it has saved an estimated 1,800 hours annually in manual logging process and loss of inaccurate planning of the manufacturing process. The company expects an annual savings of 5,000 hours in the Osaka plant, only to be compounded when the edge computing solution is rolled out to all factories across Japan.