Some time back – actually months back, ahead of Hannover Messe 2022 – Enterprise IoT Insights caught up with Sven Hamann, chief executive at Bosch Connected Industry to discuss the interplay between 5G connectivity, IoT sensing, and AI analytics as a developing Industry 4.0 platform for the firm’s own NEXEED industrial software portfolio. The trade fair references have been jettisoned, but everything else is intact, and as relevant as it was.
Hamann explains how Bosch’s broader messaging has shifted, some, as its software strategy, to bring efficiency and flexibility to factory operations, has chimed exactly with regulatory directives and urgent concern about industrial sustainability. Bosch has always sought to drive efficiencies in its own operations, he explains, as a matter of both corporate advancement and environmental responsibility; but the market also needs a green-industry champion.
Or so the argument goes. Much of the discussion is plain enough; but the story is a good one, which addresses, as well, how to sell, design, and scale Industry 4.0, and how not to get lost in the mad buzz and blind panic that surrounds environmental-digital-industrial change – to stay focused, and to make environmental concerns and business gains the same thing, effectively.
The timing of the US edition of Germany’s big Industry 4.0 trade show, Hannover Messe USA, scheduled for next week, makes for a useful, albeit coincidental and unconnected, prompt to run the interview, finally (and with apologies). So here it is: a high-level view of the state of the Industry 4.0 market, from Bosch, an elite-level, Industry 4.0 user-seller, in the home of Industrie 4.0; all the answers below are from Hamann.
…
Talk about how the Industry 4.0 story has shifted. The perception is that the appetite for digital change solutions is more acute, and growing rapidly more so – with a global pandemic, an economic downturn, and tangible environmental impacts, and more, of course. How is Bosch approaching all of this?
“The main focus for us is to help partners and customers to become more sustainable. Industry 4.0, and the whole digitalization concept, is a key enabler for sustainability. I mean, with the pandemic, there was a sense, perhaps, that the topic of climate protection went on the back-burner. But that was not the case; it has not lost any of its meaning – and, very clearly, urgency is higher than ever. And the industrial sector must play, and will play, a crucial role in environmental and climate actions.
“There have been a couple of studies on this, fairly recently. One from [consulting firm] Roland Berger about the impact on CO2 emission from different vertical domains showed the industrial and transportation sectors are major contributors. Another study from Accenture looked at which sectors can make the biggest difference, through sustainability actions, and the number on was manufacturing and production. Which fits with our personal experience, as well. Bosch was the first global industry company to become CO2-neutral, two years ago.
“And we can share that knowledge and experience with partners and customers – and Bosch Connected Industry, the software house in Bosch for industry 4.0 solutions, has this NEXEED portfolio for manufacturing and logistics to help deliver on those targets, and to support this topic of climate protection. Our energy platform (NEXEED Energy Platform) allows enterprises to monitor energy consumption – heat, power, compressed air – for a whole plant, down to individual machine level, to identify the biggest levers for sustainability.
“Another way is to reduce waste – just because, with waste, you lose on materials, and all of the energy that has gone into producing them. Less waste means less material, less production, less energy. If we can reduce scrap rates – by understanding processes and modifying tolerances, for example – then there is a direct correlation with sustainability. And we have a whole suite for maintenance management, as well – which starts with predictive maintenance, but goes up to managing a whole maintenance services team in a factory. Which is another key lever for sustainability.”
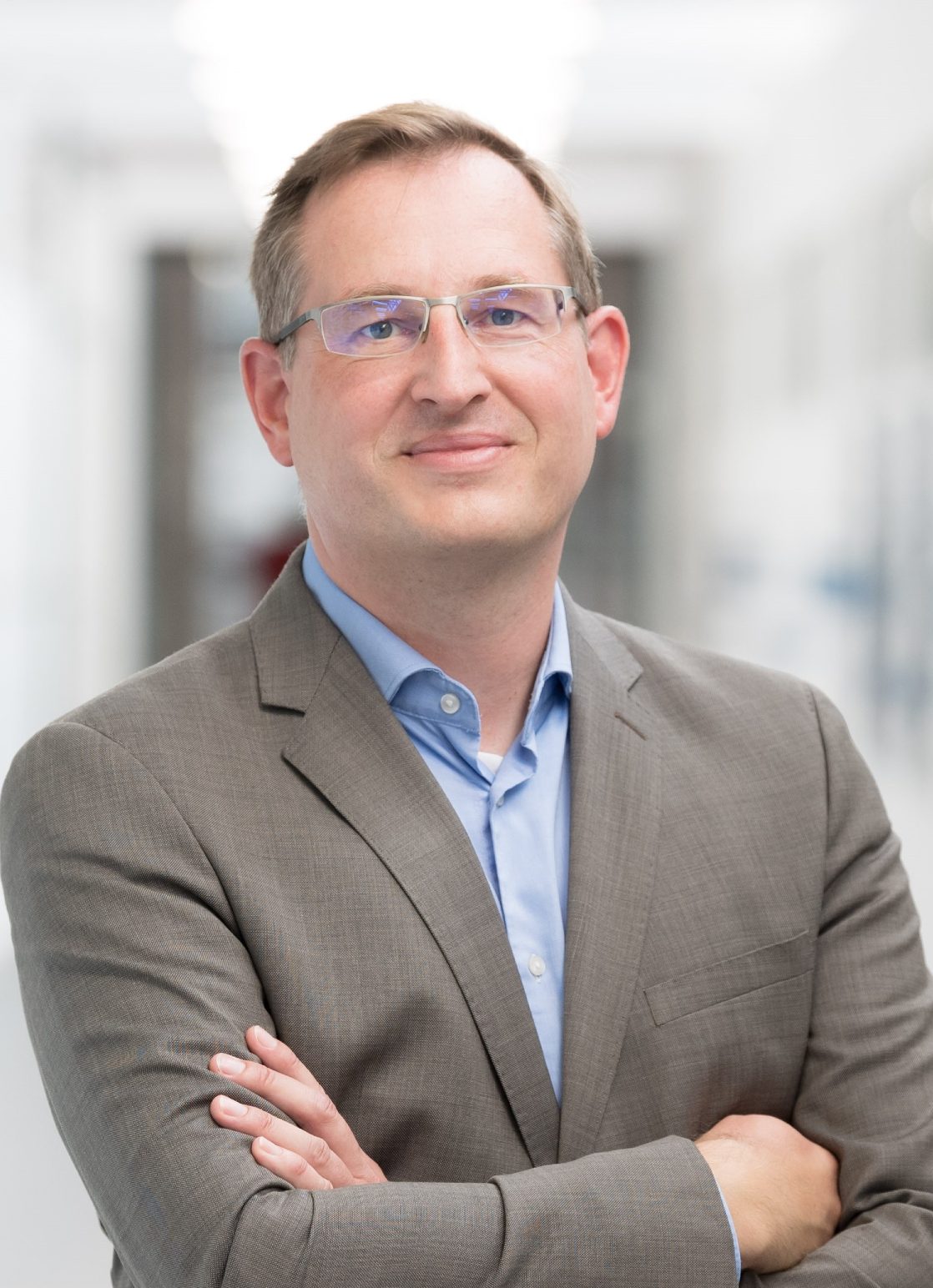
So, has the product changed or has the marketing changed? Bosch has sold predictive maintenance for years. Have the products or data outputs, say, changed, or has the marketing just shifted – to talk about sustainability?
“Both, actually. Because on one hand, we have seen, with our own experience at Bosch over the last years, that these functionalities really make a difference in factories and logistics. On the other hand, yes, you’re right; we are putting a different focus on these topics, to an extent. But that is key to the success of this. If you want to motivate enterprises to address these issues, then you have to make a stage and a show of what is important and what can be achieved. Because the industrial market has a huge responsibility, and must play a more significant role on climate protection.”
Talk briefly about how you see the opposite tech revolution – with this miniaturisation and availability of computing in IoT sensors and cloud servers, plus its distribution into edge networks, along with advances in analytics and connectivity. From an OT software point of view, are these things coming together very well, now? Bosch talks about 5G, and also AI and IoT. Which is the most critical component, as yet?
“Yes, it is very much about their combination – much more than any single one on its own. They are all important to open up new Industry 4.0 opportunities, end-to-end. I mean, 5G certainly brings opportunities to connect industry in new ways – to connect lots of devices in a large assembly hall, say; like to connect and monitor the torque in screw drivers, or to orchestrate robots and shuttles moving around. These use cases become more viable with 5G. But they all matter – it’s not about a single game-changing technology. And we are testing them all at our site in Stuttgart.”
And how does this stuff – and the Bosch software that it all supports – get into the hands of SMEs? Because, yes, Bosch has 200 factories, or whatever, and Schneider and Siemens and BMW have lots of factories, but the great industrial engine room comprises SMEs, often. So how does the Industry 4.0 story move beyond quite-wealthy big-brand manufacturing companies into the wider supply chain? How does Industry 4.0 scale – when the primary concern, often, is just to keep the lights on?
“It is a good point. On one side, the solution portfolio has to fulfil certain requirements for the wider SME market. For example, it should be quite modular – so you have the flexibility to meet the customer’s main pain points. These projects should start small, but start smart – which means beginning with a small workshop on the shop floor to identify pain points and devise a solution that delivers a short return on investment, by itself. From there, you can grow step-by-step, with a focus on rapid ROI at each step.
“What is not possible is to design a Industry 4.0 project and then wait for a big upfront investment to pay off years later. That does not make sense. It is not the way we want to work. Our focus is always to scale projects with the solutions that deliver a quick return. That is important. The other thing is you can’t just sell an Industry 4.0 solution with the instruction, ‘Hey, now do industry 4.0’. That is not going to work. So we also offer consulting on lean production – to optimise systems, reduce waste, bring intelligence. Because you can’t just sell digitalisation on top.”
And how much prep work is there just to digitise processes? Somebody said to me that, typically, the shop floor only knows these processes in their heads, or on a piece of card on the wall – that very little is actually digitised for the industrial metaverse, or whatever. Does that remain a challenge, and a big part of this Industry 4.0 consultancy?
“Yes and no. You can implement in the classic way – to assess and analyse a process, and identify ways to make it better. But of course, you quickly get to a point, as well, where you need more data. Which is when you introduce these Industry 4.0 solutions into a brown-field plant – just to get the data out of the machines. Which can be done in quite small steps. It is not rocket science to digitalize existing machines – to get more transparency about value streams, and identify key processes and key elements to make a difference.”
And when you are retrofitting brownfield machines with connectivity, is it mostly with just a Wi-Fi sensor, or a LoRaWAN sensor, or a BLE sensor, or is it sometimes now a 5G network – because, at that point, you are set to deploy a private 5G network anyway, for new machines and for some factory-of-the-future project? What are you finding?
“Yes, in the future, there will be much more usage of local 5G networks. But today: no. Industrial 5G in manufacturing is still largely in the pilot phase. And especially with SMEs, there are no 5G networks available currently. So it tends to be Wi-Fi and BLE, and lots of other different technologies; it is quite an open field.”
Talk a little more about the consultancy process, and co-creation with the customer; is this something Bosch does on its own, typically, or do you see the Industry 4.0 market increasingly coming together from across a range of disciplines?
“Generally speaking, partnership is more and more important. In industry 4.0, there are so many different technologies, and skills, and competencies, and so you can really take advantage of partnerships. It is a crucial element. Nobody should go on this journey alone. And we also believe it is also important to engage on standards and open platforms. We completely reject all kinds of isolated silo solutions or proprietary standards. We actively contribute in the Open Manufacturing Platform, and in Catena-X, and in 5G-ACIA, for example; the whole Industry 4.0 sector has to speak a common language. We won’t get to the next level going company-by-company and silo-by-silo.”