For production companies to thrive in today’s competitive market, going digital is not merely an option but a necessity. Workflows where paper still dominates are often the bottlenecks that frustrate employees. Implementation of a manufacturing execution system (MES) can help to effectively manage transformation to agile manufacturing, and drive strategic value for the organisation. But where to start? Jeroen Coussement, chief executive at Belgian industrial IoT scale-up Factry talks through the five essential steps.
To stay competitive, change is inevitable in Industry 4.0. Which is why production companies are constantly seeking innovative solutions to enhance their operational efficiency and reduce costs. One way to bridge potential gaps between the production floor and the company management, is the implementation of a Manufacturing Execution System (MES). This provides real-time data insights into production processes, quality control, traceability, and resource utilisation.
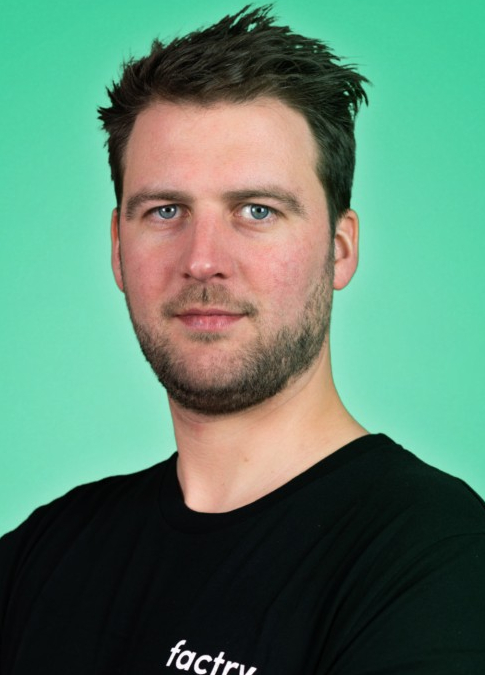
However, harnessing these advantages requires more than just industrial IoT technology – it also demands effective change management. When MES projects fail, it is usually because of a disconnect with the people involved with the change. Overcoming resistance to change, to secure fast and long-term adoption on the shop floor, is critical.
We promised you five steps to guide you through; for that, we will rely on the ADKAR model – which stands for Awareness, Desire, Knowledge, Ability, and Reinforcement. This model, developed by Jeff Hiatt in 2006, focuses primarily on individuals because successful change primarily happens at the personal level as people progress through stages of acceptance and action.
1 | Awareness (of the need for change)
Effective communication is the bedrock of successful change management. Start with ensuring that people understand why change is happening. Don’t just communicate the objectives of the implementation, but also how it will benefit the organisation, and the expected timeline. This will make employees feel more involved, and boost their motivation to adapt. For example, employees may worry about how new technology could make their jobs redundant. Tackling these issues early-on is always the best idea.
2 | Desire (to participate in change)
Stimulate a desire for change by involving employees in the development and implementation process. Allow them to voice their concerns and expectations around the MES. Show them how it will positively impact their daily tasks. For instance, show production staff how operator-friendly screens and a paperless workflow will make their day-to-day duties less stressful, reduce miscommunication, decrease errors, and improve decision-making. Workfloor ambassadors, often employees who are eager for change, can play a pivotal role to facilitate a smooth transition to a new way of working.
3 | Knowledge (about how to change)
Equip employees with the knowledge required to operate the MES effectively from the start. Provide training programs that cater to the needs of different employee groups and their specific job roles, and their digital maturity level. Training efforts should be ongoing, covering both the technical aspects of the system, and the new processes it introduces. Ensure it is hands-on, engaging, and includes practical exercises. The result: employees with enhanced skills and better problem-solving abilities. What’s not to like?
4 | Ability (to implement change)
When faced with radical change, employee fatigue can quickly set in. Thus, it is imperative to keep providing both new and current employees with the requisite training and resources to effectively navigate the MES. When employees have the ability to use the MES effectively, it becomes an integral part of their work routine, leading to improved processes and quality. In practical terms, offer continuous support and feedback, encourage peer learning, and create a helpdesk for quick issue resolution as they adapt to their new toolset.
5 | Reinforcement (to sustain change)
Once you’ve implemented the MES platform, and employees start working with the software, the job is far from over yet. Transparency and regular updates are key to sustain change. Open lines of communication remain essential. Regularly reinforce the benefits of MES through success stories, celebrate achievements, and provide continuous feedback. Monitor performance, and make improvements as necessary. By reinforcing the positive outcomes of MES, you can foster a culture of continuous improvement on the work floor, where employees actively seek ways to maximise the system’s potential. Also – don’t forget about new hires. They need to be trained too.
In general, MES implementation is more than just a technological upgrade. It is a cultural shift within the organisation. Giving employees the right tools goes a long way, but it’s not just about immediate gains but also long-term success. Change is carried out best when openly supported by the leadership team, as their endorsement signals MES implementation is a top priority. Leadership support ensures that the MES remains a strategic asset, and keeps evolving to meet changing business needs.
In conclusion, a robust change management strategy is essential to pave the way for a smooth transition to agile manufacturing, and realise the full potential of your MES software. Navigating an MES implementation, including change management, may be a complex endeavour at times. Yet, it is also one that can transform production processes and boost competitiveness substantially. As you embark on this journey, be sure to have an experienced partner at your side, that not only delivers a cutting-edge MES solution, but also has an eye for your people. After all, the shop floor is where it all happens.
About the author
Jeroen Coussement is the CEO of Factry. Headquartered in Ghent, Belgium, Factry helps process industry customers create clarity using IIoT solutions that digitize production activities and increase effectiveness. The scale-up brings its solutions and open data culture to companies—from SMEs to multinationals—on five continents and in 28 countries. Visit Factry.io to learn more.